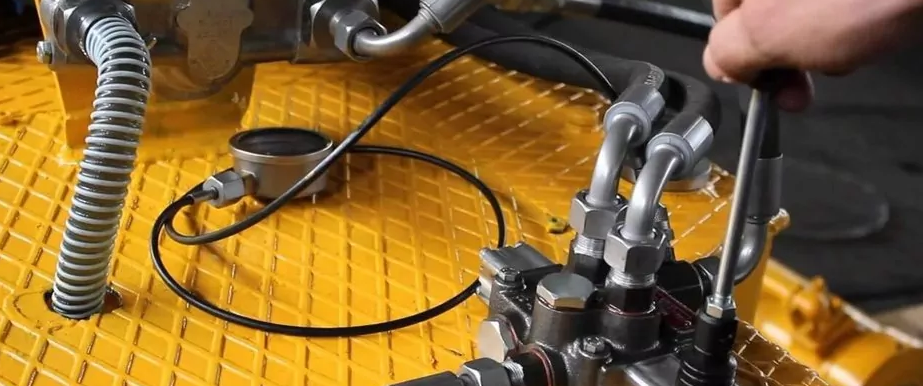
Важной составляющей технического обслуживания является своевременное обнаружение неисправностей, приведших к потере работоспособности оборудования и поиск отказавшего элемента. Для сложных гидроприводов это оказывается достаточно трудоемкой процедурой и может вызвать длительный простой оборудования.
Метод простого перебора или метод проб и ошибок, практически, неприемлем хотя бы из-за длительности по времени и значительной дороговизны.
Наиболее правильным для выявления неисправного элемента гидросистемы является использование логического метода поиска, что требует хороших знаний принципов действия, конструкции и особенностей функционирования всех гидроаппаратов по отдельности и системы в целом.
Вполне понятно, что если все элементы системы оснащены устройствами, которые дают информацию об их техническом состоянии (датчики усилий, скорости, перемещений, давления, уровня, температуры и др.), то проблемы поиска неисправностей не возникает. Каждый отказ обнаруживается автоматически. Однако подобная ситуация может быть реализована только для очень ответственных и дорогих гидросистем автоматизированных машин. Поэтому логический метод диагностики может быть применен для большинства существующих гидросистем различной степени сложности.
Логический метод диагностики гидравлических систем
Весь процесс поиска неисправностей разбивается на последовательные шаги: вначале устанавливается вид функциональной неисправности всей гидросистемы (или всего гидропривода), затем конкретизируется группа гидроаппаратов, неисправности, которых могут быть причиной функциональных отказов. При этом используется опыт, накопленный при эксплуатации данной системы, либо систем, косвенно похожих на диагностируемую. После этого выявляется неисправный аппарат, определяется вид неисправности и принимается решение о способе ее устранения. Таким образом, процедуру поиска «виновника» отказа в гидравлической системе любого технологического оборудования можно представить в виде определенной последовательности действий.
Общий смысл этих действий представляет собой совокупность следующих шагов.
Шаг 1. Уточнение возникшей неисправности в машине (конкретизируется вид функциональной неполадки).
При этом используется перечень проявлений неисправностей:
- прекращение движения рабочего органа машины;
- неконтролируемое движение рабочего органа;
- недостаточная скорость перемещения;
- недостаточное усилие, развиваемое рабочим органом;
- разрыв трубопровода или РВД;
- нагрев рабочей жидкости;
- появление пены в баке;
- - еправильное направление движения.
После установления и четкого формулирования вида неисправности, на основании гидравлической схемы, собственного опыта и описания рабочего процесса определяется, какой из основных параметров гидросистемы является причиной этой неисправности: давление, расход или направление потока рабочей жидкости.
Шаг 2. Составление предварительного перечня гидроаппаратов и элементов системы, подозреваемых в создании неисправности.
Составляется перечень гидроаппаратов, которые непосредственно участвуют в передаче мощности к исполнительному механизму, нарушение работоспособности которого было выявлено на первом шаге, а также в управлении этой мощностью.
Шаг 3. Анализ статистической информации причин неисправности.
Изучается статистическая информация по неполадкам и техническому обслуживанию конкретной гидросистемы или ее аналогов. Обычно такая информация содержится в техническом описании машины и, главным образом, в журнале учета неисправностей гидрооборудования. На практике встречается редко.
Шаг 4. Интуитивный поиск неисправности.
Интуитивная оценка ситуации проводится с целью сокращения числа подозреваемых элементов. Для этого — на слух (повышенный шум при работе), на ощупь (локальный нагрев гидроаппаратов), визуально (потеки масла, состояние агрегатов) — ищутся дополнительные признаки неисправности какого-либо гидроаппарата или потери рабочей жидкостью своих эксплуатационных качеств, например повышенные шум, вибрация, нагрев корпуса, пенообразование, ненормальный уровень жидкости в баке и т.д.
Шаг 5. Поиск неисправности с помощью технических средств.
Производится в тех случаях, когда причина неисправности не была выявлена на шагах 3 и 4. Используются специальные контрольно-измерительные средства для определения давления и расхода жидкости, величины хода штока гидроцилиндра, положения золотника распределителя и других параметров гидросистемы и ее элементов. Наиболее достоверный способ.
При этом бывает весьма желательно осуществлять такой контроль без демонтажа компонентов гидросистемы. Для этого сама система должна быть оборудована устройствами для легкого присоединения контрольных средств и приборов. Для контроля расхода приходится разъединять соединительную аппаратуру (контрольные точки позволяют измерить давление).
Шаг 6. Выявление неисправного аппарата, определение неисправности и принятие решения о способе ее устранения.
На основании выявленных признаков неисправности формулируется окончательный вывод о «виновности» конкретного гидроаппарата и принимается решение о возможности устранения неисправности на месте, либо о замене его новым.
Например, не выдвигается шток гидроцилиндра из-за несрабатывания клапана последовательности. Если, запорный элемент клапана заклинен в закрытом положении вследствие поломки пружины, то необходима замена неисправного клапана новым.
В случае если неисправность клапана обусловлена его загрязнением, то его прочистку можно провести на месте.
При неисправностях насоса, износе гидроцилиндра или гидрораспределителя, как правило, их заменяют на новые, а неисправные отправляют в ремонт.
Шаг 7. Анализ причин появления отказа и возможных последствий неисправности.
Проводится анализ общих причин, которые могли предшествовать появлению отказа, чтобы предотвратить появление подобных отказов в дальнейшем. Например, если отказ был связан с засоренностью аппарата, а уровень загрязненности рабочей жидкости близок к критическому, то следует ожидать возникновение последующих отказов.
После выхода из строя насоса вся система до установки нового насоса должна быть тщательно промыта для удаления возможных обломков и мелких частиц.
Обязательным при этом является внесение информации о неисправности в журнал учета.
Для сложных гидросистем целесообразно разрабатывать специальные алгоритмы поиска неисправностей и рекомендации по устранению причин их возникновения, а также оптимальные графики проведения планово-предупредительных проверок и ремонтов.
Своевременное устранение постепенных отказов и причин их возникновения позволяет предотвратить появление внезапных отказов с прекращением функционирования всего гидропривода.
Устранение причин появления постепенных отказов — основная задача технического обслуживания гидросистем.
Технический метод диагностики гидравлических систем
В решении проблемы обеспечения надежной работы гидроприводов постоянно возрастает роль технической диагностики, контролирующей техническое состояние гидропривода в процессе эксплуатации, что позволяет использовать привод оптимальным образом, осуществлять ремонт в кратчайшие и действительно необходимые сроки.
В качестве переносных средств технической диагностики все более широко применяются гидротестеры, с помощью которых можно контролировать давление, температуру и расход. В состав таких тестеров входят: один-два датчика давления, или малогабаритный манометр, средства сопряжения, датчик температуры, вторичный прибор для цифровой индикации контролируемых параметров, расходомер.
К встраиваемым средствам диагностики относятся различные датчики и индикаторы, которые позволяют оперативно следить за техническим состояние привода. Особенно перспективно использование встроенных в различные участки гидросистемы тепловых датчиков, с помощью которых реализуется термодинамический метод диагностирования
- по температуре масла в различных точках гидросистемы можно судить о величине и направлении потоков, наличии гидравлических потерь, эффективности системы терморегулирования.
Перспективно применение средств вибрационной диагностики, позволяющих по вибрациям корпусов насосов производить оперативный анализ нормированных диагностических признаков, свидетельствующих о наличии погрешностей деталей или их взаимного расположения после сборки, и отбраковывать насосы по комплексному показателю качества.
Гидравлическое оборудование в Казахстане
Источник: ts.by